Achieving optimal performance with aerosol actuator is crucial for industries that rely on these devices for efficient and accurate delivery of various products. Whether it’s pharmaceuticals, household products, or automotive applications, the performance of aerosol actuators can significantly impact overall user satisfaction and brand reputation. In this article, we delve into the key factors that influence the performance of aerosol actuators and explore how brands can enhance their effectiveness.
From nozzle design to valve functionality, there are several elements that contribute to the performance of aerosol actuators. Understanding the intricate details of these components is essential for manufacturers looking to deliver superior results. Additionally, optimizing actuator performance can help brands differentiate their products in a highly competitive market.
By implementing cutting-edge technologies and rigorous testing methodologies, brands can ensure that their aerosol actuators provide consistent dosage, controlled spray pattern, and efficient product dispensing. Moreover, brands that prioritize user experience through ergonomically designed actuators can enhance usability and customer satisfaction.
Join us as we explore the various aspects of aerosol actuator performance and discover the strategies to achieve optimal results. Whether you are a manufacturer or a consumer, understanding the mechanics behind these devices can lead to more effective use and improved product performance.
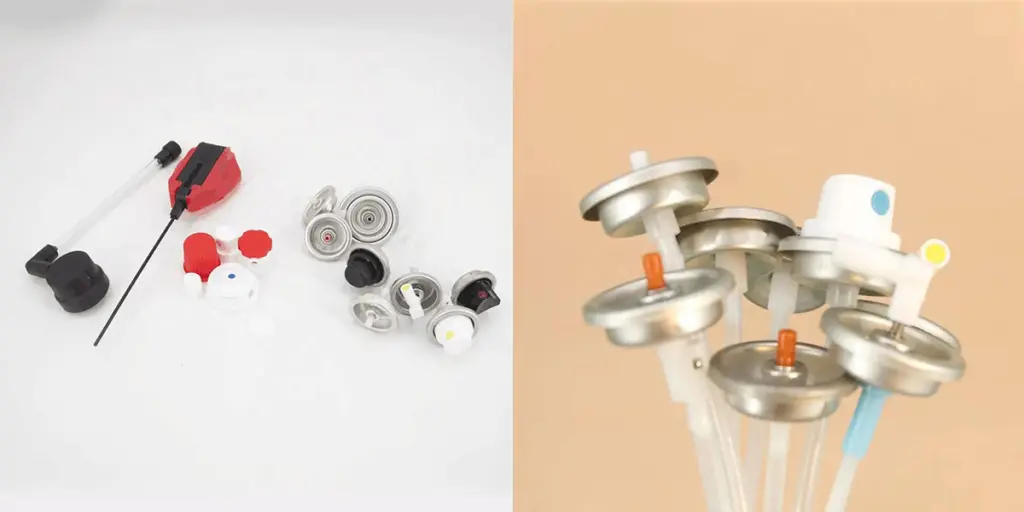
The importance of aerosol actuator performance
One of the main reasons performance is critical for aerosol actuators is to ensure consistent and precise delivery of the target product. For example, in aerosol cans used for lubricating oil, reliable actuators are crucial for accurate application of lubricating oil. In industries such as cosmetics and homewares, consistency in spray pattern and dosage is equally important to ensure product effectiveness and user satisfaction.
An efficient and well-designed aerosol actuator not only helps deliver the right amount of product but also minimizes waste. They prevent overuse or spillage, reducing unnecessary costs and environmental impact. Additionally, well-performing actuators are user-friendly, making the product more accessible and intuitive to use by a wide range of consumers.
In summary, the importance of aerosol actuator performance cannot be overstated. It affects the functionality, accuracy and user-friendliness of aerosol products across industries
Factors Affecting Performance in Aerosol Actuators
The performance of aerosol actuators, critical in ensuring the precise and efficient dispensing of aerosol products, can be influenced by several factors. Understanding these factors is essential for optimizing the performance of aerosol actuators across various applications.
- Actuator Design: The design of the actuator itself is a key factor. Factors like nozzle shape, size, and material can impact the spray pattern, droplet size, and dispensing accuracy. A well-engineered actuator design is crucial for achieving the desired product performance.
- Propellant Type: The type of propellant used in the aerosol product can affect actuator performance. Propellants influence the pressure and flow rate, which in turn impact the consistency and effectiveness of product delivery.
- Formulation of the Product: The composition of the product being dispensed also plays a role. The viscosity, density, and chemical properties of the product can influence the ease of dispensing and the need for specialized actuators to accommodate different product types.
- Environmental Conditions: Factors like temperature and humidity can affect the performance of aerosol actuators. Extreme conditions may alter the pressure, spray pattern, or the product’s behavior, requiring adjustments to the actuator design or formulation.
- Actuator Maintenance: Regular maintenance and cleaning of aerosol actuators are essential to prevent clogging or deterioration over time. A well-maintained actuator ensures consistent performance and product quality.
- Manufacturing Quality: The precision and quality of the manufacturing process for both the actuator and the aerosol product itself are critical. Any variations in production can lead to inconsistencies in performance.
- User Behavior: Finally, how users handle the aerosol product and actuator can impact performance. Incorrect usage, such as holding the canister at the wrong angle or shaking it improperly, can lead to suboptimal dispensing.
Factors Affecting Performance in Aerosol Actuators
The performance of aerosol actuators, critical in ensuring the precise and efficient dispensing of aerosol products, can be influenced by several factors. Understanding these factors is essential for optimizing the performance of aerosol actuators across various applications.
- Actuator Design: The design of the actuator itself is a key factor. Factors like nozzle shape, size, and material can impact the spray pattern, droplet size, and dispensing accuracy. A well-engineered actuator design is crucial for achieving the desired product performance.
- Propellant Type: The type of propellant used in the aerosol product can affect actuator performance. Propellants influence the pressure and flow rate, which in turn impact the consistency and effectiveness of product delivery.
- Formulation of the Product: The composition of the product being dispensed also plays a role. The viscosity, density, and chemical properties of the product can influence the ease of dispensing and the need for specialized actuators to accommodate different product types.
- Environmental Conditions: Factors like temperature and humidity can affect the performance of aerosol actuators. Extreme conditions may alter the pressure, spray pattern, or the product’s behavior, requiring adjustments to the actuator design or formulation.
- Actuator Maintenance: Regular maintenance and cleaning of aerosol actuators are essential to prevent clogging or deterioration over time. A well-maintained actuator ensures consistent performance and product quality.
- Manufacturing Quality: The precision and quality of the manufacturing process for both the actuator and the aerosol product itself are critical. Any variations in production can lead to inconsistencies in performance.
- User Behavior: Finally, how users handle the aerosol product and actuator can impact performance. Incorrect usage, such as holding the canister at the wrong angle or shaking it improperly, can lead to suboptimal dispensing.
The type of aerosol actuator selected significantly affects the performance of the aerosol product. Different actuator types are designed to meet specific application requirements such as accurate dosing, uniform coverage, foam generation, concentrated flow and adjustable spray patterns.
Common Performance Issues in Aerosol Actuators and How to Troubleshoot Them
Aerosol actuators can encounter various performance issues that may affect the functionality and user experience. Understanding these common issues and how to troubleshoot them can help ensure consistent and reliable aerosol product performance:
- Clogging: Clogging in the actuator nozzle or valve is a common issue, often caused by dried product residue or particles. To troubleshoot, try cleaning the actuator by removing it and using warm water or a solvent to clear the blockage. Regular maintenance can prevent clogging.
- Uneven Spray Pattern: An uneven or erratic spray pattern can lead to wasted product and uneven coverage. To address this issue, ensure that the actuator nozzle is clean and free from obstructions. Check for damaged or misaligned components and replace them if necessary.
- Leaking: Product leaking from the actuator or valve can be a messy problem. Leaks may occur due to a damaged or improperly seated gasket or valve. To troubleshoot, inspect the gasket and valve for damage, replace them if needed, and ensure they are correctly installed.
- Inconsistent Dosage: In medical or precision applications, inconsistent dosage can be a serious concern. This issue may result from improper actuator design, wear and tear, or manufacturing defects. Troubleshoot by using a quality-controlled actuator specifically designed for metered-dose applications.
- Blocked or Stuck Actuator: Sometimes, the actuator may become blocked or stuck in the down position, preventing product dispensing. To address this issue, check for obstructions or damage to the actuator components, and gently free any stuck parts.
- Difficulty in Operation: Users may face difficulty in operating the actuator, particularly with trigger sprayers or manual pump sprayers. Ensure that the actuator is assembled correctly and that it is not over-tightened, which can impede its functionality.
- Environmental Factors: Changes in temperature and humidity can affect the performance of aerosol actuators. When exposed to extreme conditions, the actuator’s behavior may alter. Storing aerosol products in a controlled environment can mitigate these effects.
Regular maintenance, quality control, and using the right type of actuator for the application are key strategies to troubleshoot and prevent common performance issues in aerosol actuators.
Case Studies Showcasing Improved Performance with Aerosol Actuators
Several case studies across various industries demonstrate the significant impact of using high-quality aerosol actuators on product performance and user experience:
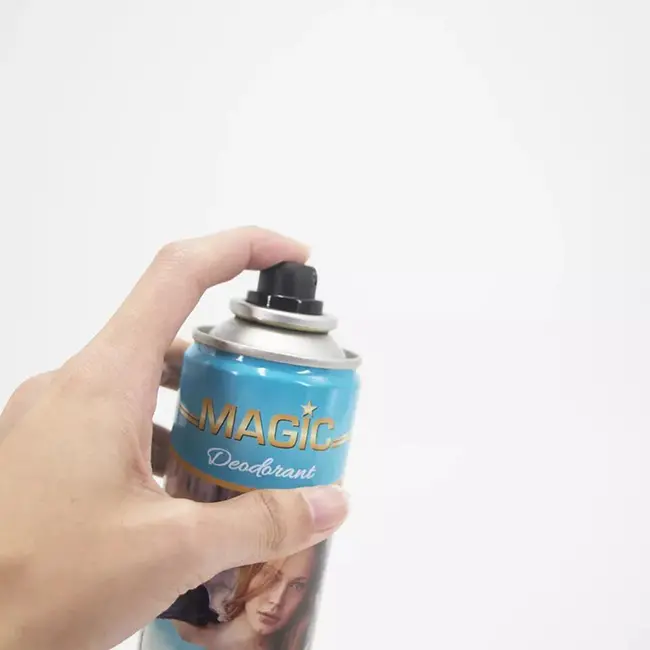
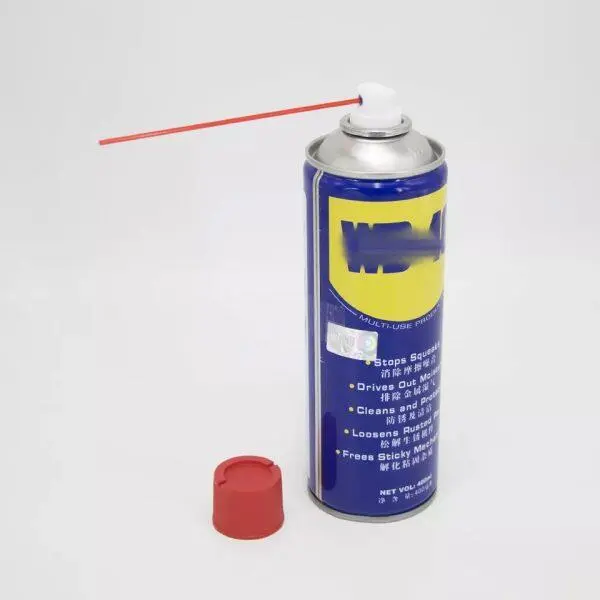
- Medical Inhalers: In the field of healthcare, medical inhalers are a critical application where precise dosage and consistent performance are paramount. Case studies have shown that the use of advanced metered-dose aerosol actuators has led to improved patient outcomes. These actuators ensure accurate dosing and a reliable aerosol dispersion, resulting in enhanced drug delivery and better disease management for patients.
- Personal Care Products: Brands in the personal care industry have reported improved consumer satisfaction and product efficacy by utilizing spray actuators with well-engineered spray patterns. The consistency and coverage of the spray pattern have been enhanced, leading to more even application of products like hair sprays, deodorants, and sunscreens.
- Cleaning Products: Household and industrial cleaning products have benefited from the use of efficient aerosol actuators. Case studies have demonstrated that high-quality actuators lead to more controlled streams or sprays, reducing product waste and ensuring targeted application. This results in cost savings and improved cleaning efficiency.
- Automotive and Lubricant Products: In automotive and industrial applications, nozzle caps and aerosol actuators have been instrumental in delivering the right amount of lubricant or adhesive precisely where needed. Case studies have highlighted the importance of these actuators in ensuring accurate and controlled product application, minimizing excess waste and enhancing machinery performance.
These case studies underscore the importance of selecting the appropriate aerosol actuators for specific applications. By doing so, companies can achieve superior product performance, user satisfaction, and cost-efficiency, ultimately leading to improved outcomes and benefits across a range of industries.
Summarize
Fanxun has more than 10 years of industry experience, focusing on capping systems for the packaging and bottling industry. We provide professional services to all our valued customers, shipping to more than 30 countries, depending on your needs and production system, you will find the best accessories for your business. At Fanxun, you can choose from a number of options designed by the best experts who will strive to package your product with precision and care to make your product stand out in the market.