Üretici olarak, ensuring product quality is critical to building a loyal customer base and staying ahead of the competition. One way to improve product quality is to use induction sealing gaskets. In this ultimate guide, we’ll walk you through everything you need to know about induction seal liners and how they can improve your manufacturing process.
Induction seal liners are an effective packaging solution that provide an airtight seal for your products, preventing leakage, contamination and tampering. By using induction heating, these liners create a strong seal between the cap and container, ensuring product freshness and integrity.
It not only improves product quality but also brings many benefits to manufacturers. From extending shelf life to increasing brand loyalty and customer satisfaction, the benefits of incorporating it into packaging are undeniable.
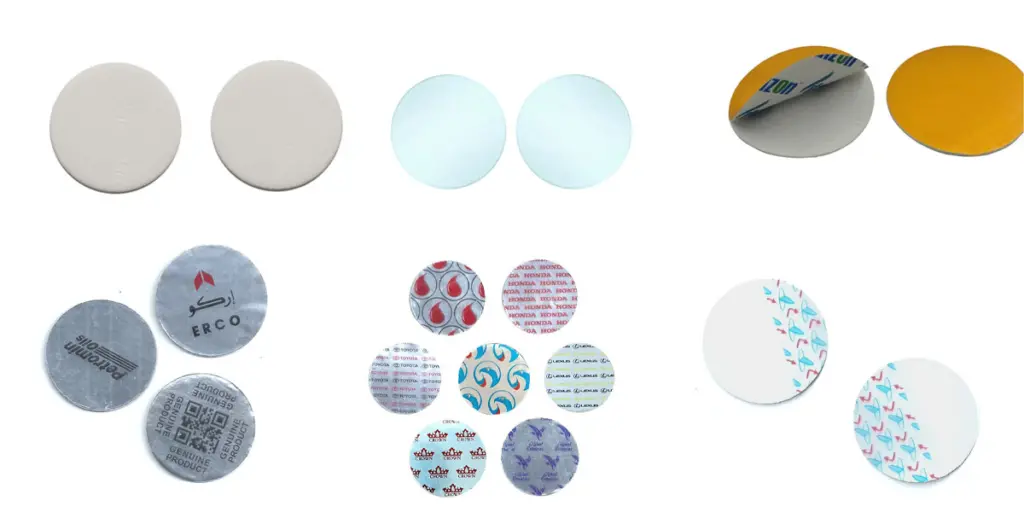
What are induction seal liners?
Induction seal liners are a common type of liner used in bottle caps and closures. They consist of a foil or laminate material that is sealed onto the mouth of a bottle using electromagnetic induction. The liner creates a hermetic seal, providing a tamper-evident barrier that prevents leaks, contamination, and product tampering.
The induction sealing process involves placing the cap with the liner onto the bottle, and then passing it under an induction sealing machine. The machine generates an electromagnetic field that heats the foil liner, causing it to bond to the bottle’s rim. This creates a secure and tamper-evident seal that remains intact until the consumer opens the bottle for the first time.
Induction seal liners are commonly used in various industries, including pharmaceuticals, food and beverages, makyaj malzemeleri, and chemicals. They offer several benefits, such as extending product shelf life, ensuring product freshness, preventing leaks and spills, and providing a visual indicator of tampering.
Etraflı, induction seal liners are an effective and widely used packaging solution for ensuring product integrity and consumer safety. They provide a reliable barrier against contamination and tampering, while also offering convenience and peace of mind for both manufacturers and consumers.
Benefits of using induction seal liners
- 1. Tamper-evident protection: Induction seal liners provide a visible indication of tampering, ensuring consumer safety and product integrity. The liner creates a hermetic seal that cannot be easily opened or resealed without leaving visible evidence of tampering. This gives consumers confidence in the safety and authenticity of the product.
- 2. Extended product shelf life: The hermetic seal formed by induction seal liners helps to extend the shelf life of various products. It prevents air, nem, and other contaminants from entering the bottle, which can cause spoilage, oxidation, or degradation of the product. By creating a barrier against external factors, the induction seal liner helps to maintain product freshness and quality.
- 3. Leakage prevention: Induction seal liners provide a reliable and leak-proof closure, reducing the risk of spills and leaks during storage, toplu taşıma, and handling. The liner adheres tightly to the bottle’s rim, preventing any liquid from escaping or seeping out. This is especially important for products that are prone to leakage, such as liquids or viscous substances.
- 4. Improved product safety: Induction seal liners offer an additional layer of safety for products that are potentially hazardous or sensitive to contamination. They act as a barrier, preventing any foreign particles, bakteriler, or contaminants from entering the bottle and compromising the product’s safety or effectiveness. This is particularly important in industries such as pharmaceuticals and chemicals, where product safety is paramount.
- 5. Consumer convenience: Induction seal liners are designed for easy removal by the end-user. Once the liner is broken or peeled off, it reveals a clean and untouched product surface. This convenience factor enhances the user experience and ensures that the product is easy to access and use.
Etraflı, induction seal liners provide multiple benefits for packaging applications. They offer tamper-evident protection, extend product shelf life, prevent leakage, enhance product safety, and provide convenience for both manufacturers and consumers. Their versatility and effectiveness make them a popular choice for a wide range of industries.
How induction seal liners work
Induction seal liners work based on the principle of electromagnetic induction. The liner is composed of a layer of aluminum foil, often laminated with a layer of polymer material. The foil layer acts as a conductor of heat, while the polymer layer provides adhesion and stability.
The sealing process begins by placing the cap with the induction seal liner onto the bottle or container. The bottle then passes under an induction sealing machine, which generates an electromagnetic field. When the bottle reaches the sealing head of the machine, the electromagnetic field interacts with the foil layer of the induction seal liner.
The electromagnetic field induces electrical currents within the foil layer, causing it to heat up rapidly. The heat is transferred to the polymer layer, which softens and melts, adhering to the rim of the bottle or container. As the heat dissipates, the polymer solidifies, creating a hermetic seal that is resistant to air, nem, and contaminants.
The ability of the foil layer to heat rapidly is due to its electric resistance, which creates heat through the interaction with the electromagnetic field. The rapid heating and cooling process ensures a strong bond between the liner and the bottle, creating a tamper-evident and leak-proof seal.
The induction seal liner provides a secure closure that is difficult to tamper with without leaving evidence of tampering. To access the product, the consumer needs to break or peel off the liner, revealing a fresh and untouched product surface.
Etraflı, the use of electromagnetic induction in the sealing process allows for efficient and reliable sealing of bottles and containers, ensuring product integrity, security, and freshness.
Different types of induction seal liners
- Different types of induction seal liners:
- One-piece liners: This type of liner is made of a single material, typically a polymer such as polyethylene foam or polyurethane foam. One-piece liners provide a secure seal and are easy to remove, making them suitable for a wide range of applications.
- Two-piece liners: Two-piece liners consist of two layers, with a foil layer bonded to a polymer layer. The foil layer provides the heat-conductive and tamper-evident properties, while the polymer layer offers adhesion and stability. Two-piece liners offer enhanced seal integrity and are often used for products that require a higher level of protection or are more sensitive to contamination.
- Venting liners: Venting liners include a vent or venting system to release excess pressure or gas buildup inside the bottle or container. This is particularly important for products that undergo changes in temperature or pressure during storage or transportation. Venting liners help prevent bottle deformation or leakage by allowing controlled release of pressure without compromising the seal integrity.
- Peelable liners: Peelable liners are designed to be easily peeled off from the bottle, leaving a clean product surface. They offer convenience and are commonly used for products that require frequent access, such as cosmetics, creams, or lotions. Peelable liners can be made from various materials, including foils, films, or laminates, depending on the specific application requirements.
- Tamper-evident liners: Tamper-evident liners provide visual indications of tampering, ensuring product safety and integrity. These liners can include features such as breakable seals, holographic patterns, or unique patterns that show visible evidence of tampering. Tamper-evident liners are widely used in industries where product authenticity and safety are crucial, such as pharmaceuticals or food and beverages.
- Printed liners: Printed liners can include branding, ürün bilgileri, or safety warnings printed directly onto the liner material. This allows manufacturers to provide additional information or enhance the visual appeal of the packaging. Printed liners can be customized to match branding requirements and contribute to a cohesive packaging design.
- Different types of induction seal liners offer specific benefits and are suitable for various applications. Manufacturers can choose the appropriate liner based on the product requirements, desired level of tamper-evidence, convenience, and branding considerations.
Different types of induction seal liners offer specific benefits and are suitable for various applications. Manufacturers can choose the appropriate liner based on the product requirements, desired level of tamper-evidence, convenience, and branding considerations.
Factors to consider when choosing induction seal liners
- 1. Material compatibility: Ensure that the induction seal liner material is compatible with the formulation and properties of the product being packaged. It should be resistant to chemical interactions, nem, and other factors that could compromise the integrity, kalite, or safety of the product.
- 2. Seal integrity: Evaluate the sealing performance of the induction seal liner, including its ability to create a hermetic seal and prevent leakage or contamination. Consider factors such as the liner’s adhesion strength, compatibility with different container materials, and resistance to temperature changes or pressure differentials.
- 3. Tamper-evident features: If tamper-evidence is a requirement for your product, consider liners that offer visible indicators of tampering, such as breakable seals or holographic patterns. These features provide assurance to consumers that the product has not been tampered with.
- 4. Ease of removal: Evaluate the ease of removing the induction seal liner by the end-user. It should be convenient without requiring excessive force or specialized tools. Consider factors such as peelability, tear resistance, and whether the liner leaves any residues on the bottle after removal.
- 5. Venting capabilities: For products that may undergo pressure or gas buildup, such as carbonated beverages or volatile substances, consider venting liners. These liners allow controlled release of pressure, preventing bottle deformation or leakage.
- 6. Printing options: If branding or product information is important, explore options for printed liners. Customizable printed liners can enhance the visual appeal of the packaging, provide branding opportunities, and deliver additional information to consumers.
- 7. Regulatory compliance: Ensure that the chosen induction seal liner complies with relevant safety regulations and industry standards. Consider factors such as child-resistant packaging requirements, proper labeling, and any specific standards for your product category.
Factors to consider when choosing induction seal liners:
- Material compatibility: Ensure that the induction seal liner material is compatible with the formulation and properties of the product being packaged. It should be resistant to chemical interactions, nem, and other factors that could compromise the integrity, kalite, or safety of the product.
- Seal integrity: Evaluate the sealing performance of the induction seal liner, including its ability to create a hermetic seal and prevent leakage or contamination. Consider factors such as the liner’s adhesion strength, compatibility with different container materials, and resistance to temperature changes or pressure differentials.
- Tamper-evident features: If tamper-evidence is a requirement for your product, consider liners that offer visible indicators of tampering, such as breakable seals or holographic patterns. These features provide assurance to consumers that the product has not been tampered with.
- Ease of removal: Evaluate the ease of removing the induction seal liner by the end-user. It should be convenient without requiring excessive force or specialized tools. Consider factors such as peelability, tear resistance, and whether the liner leaves any residues on the bottle after removal.
- Venting capabilities: For products that may undergo pressure or gas buildup, such as carbonated beverages or volatile substances, consider venting liners. These liners allow controlled release of pressure, preventing bottle deformation or leakage.
- Printing options: If branding or product information is important, explore options for printed liners. Customizable printed liners can enhance the visual appeal of the packaging, provide branding opportunities, and deliver additional information to consumers.
- Regulatory compliance: Ensure that the chosen induction seal liner complies with relevant safety regulations and industry standards. Consider factors such as child-resistant packaging requirements, proper labeling, and any specific standards for your product category.
By considering these factors, businesses can select induction seal liners that offer optimal sealing performance, tamper-evident features, kullanım kolaylığı, and compliance with regulations, ultimately ensuring the integrity and safety of the packaged product.
Çözüm:
Induction seal liners play a crucial role in ensuring product quality, emniyet, and integrity. By providing a hermetic seal, they prevent leaks, contamination, and tampering, protecting the product throughout its lifecycle. With their tamper-evident features, induction seal liners offer reassurance to consumers and help build trust in the brand.
Etraflı, induction seal liners are a valuable tool for maximizing product quality and ensuring consumer satisfaction. By investing in the right sealing technology and considering various factors, businesses can enhance their packaging solutions and deliver products that meet the highest quality standards.