Nếu bạn đã từng tự hỏi làm thế nào để làm cho một hộp thiếc bền và đáng tin cậy, Sau đó, hướng dẫn thiết yếu này là dành cho bạn. Trong bài viết này, Chúng tôi đưa bạn qua tất cả các khía cạnh của Tin có thể thành phần và cung cấp một cái nhìn sâu sắc về các kỹ thuật sản xuất khác nhau được sử dụng trong sản xuất thiếc có thể, bao gồm cả việc cắt, hình thành và niêm phong. Hiểu các quy trình này sẽ cung cấp cho bạn sự hiểu biết đầy đủ về cách thực hiện lon thiếc và tại sao chúng là một trong những lựa chọn phổ biến nhất để đóng gói nhiều loại hàng hóa khác nhau.
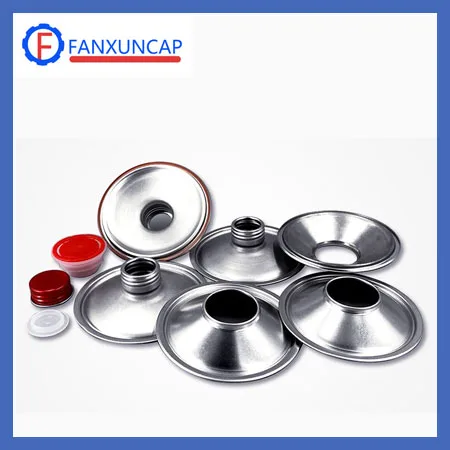
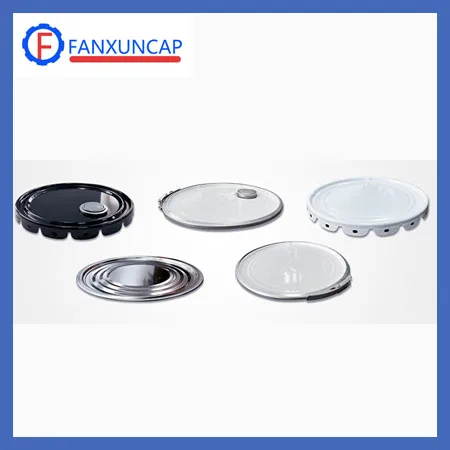
Quá trình sản xuất các thành phần có thể
Lon thiếc được sản xuất thông qua một loạt các quy trình chính xác và phức tạp. Bước đầu tiên trong quy trình sản xuất là cắt các tấm bằng thiếc thành kích thước và hình dạng mong muốn. Điều này thường được thực hiện bằng cách sử dụng các máy cắt tốc độ cao để đảm bảo độ chính xác và hiệu quả. Khi các tấm được cắt, Chúng được định hình thành các thân xe bằng cách sử dụng các thiết bị chuyên dụng. Các cạnh của thân hộp sau đó được cuộn tròn để tạo ra một lớp hoàn thiện mịn màng và an toàn.
Sau khi cơ thể có thể được hình thành, Các đầu được gắn bằng máy may. Quá trình này liên quan đến việc gấp và uốn các cạnh của thân thể và có thể kết thúc với nhau để tạo ra một con dấu an toàn. Quá trình đường may rất quan trọng đối với tính toàn vẹn của hộp thiếc, vì bất kỳ sự không hoàn hảo nào cũng có thể làm tổn hại con dấu và dẫn đến rò rỉ hoặc ô nhiễm.
Tầm quan trọng của độ bền của thiếc có thể đóng gói
Độ bền là một yếu tố chính trong sự thành công của bao bì có thể đóng gói. Lon thiếc thường được sử dụng để lưu trữ và vận chuyển nhiều loại sản phẩm, Từ thực phẩm và đồ uống đến hóa chất và mỹ phẩm. Độ bền của lon thiếc đảm bảo rằng nội dung được bảo vệ khỏi các yếu tố bên ngoài như độ ẩm, Không khí và ánh sáng, có thể gây ra hư hỏng hoặc suy thoái.
Vật liệu sản xuất
Một trong những người đóng góp chính cho độ bền của lon thiếc là các vật liệu được sử dụng. Thép và nhôm là vật liệu được sử dụng phổ biến nhất để sản xuất lon thiếc. Thép được biết đến với sức mạnh và khả năng chống va đập, Làm cho chúng trở nên lý tưởng cho hàng hóa đóng gói yêu cầu bảo vệ thêm. Lon nhôm, mặt khác, nhẹ và chống ăn mòn, làm cho chúng trở thành một lựa chọn phổ biến cho đồ uống.
Lớp phủ bên trong
Ngoài các vật liệu, Lớp phủ bên trong của tấm thiếc cũng có thể đóng một vai trò quan trọng trong việc đảm bảo độ bền. Những lớp phủ này bảo vệ nội dung của lon khỏi tiếp xúc trực tiếp với kim loại, Ngăn chặn các phản ứng hóa học có thể ảnh hưởng đến chất lượng sản phẩm. Những lớp phủ này cũng ngăn chặn độ ẩm và oxy, tiếp tục kéo dài tuổi thọ của lon.
Các loại thành phần có thể
Lon thiếc được tạo thành từ nhiều thành phần làm việc cùng nhau để cung cấp một giải pháp bao bì chắc chắn. Các thành phần chính của A có thể bao gồm cơ thể, có thể và đường may. Mỗi thành phần có một chức năng cụ thể góp phần vào độ bền và độ tin cậy tổng thể của gói.
Bể là thùng chứa chính để giữ sản phẩm. Nó thường có hình dạng hình trụ và được làm bằng một ống rỗng được làm từ một miếng thiếc. Cơ thể cung cấp tính toàn vẹn cấu trúc của hộp thiếc, đảm bảo nó có thể chịu được việc xử lý và vận chuyển.
Các đầu của hộp thiếc chịu trách nhiệm niêm phong container và giữ an toàn cho nội dung. Có hai loại nắp thường được sử dụng cho hộp thiếc có thể đóng gói: nắp đậy dễ dàng và nắp truyền thống. Mở dễ dàng được trang bị tab kéo hoặc dải nước mắt để dễ dàng truy cập vào các vật phẩm. Kết thúc truyền thống, mặt khác, yêu cầu một dụng cụ mở có thể mở.
Đường may của một hộp thiếc là nơi cơ thể và có thể kết hợp với nhau. Quá trình đường may đảm bảo một liên kết chặt chẽ và mạnh mẽ giữa các thành phần, ngăn chặn bất kỳ rò rỉ hoặc ô nhiễm nào. Chất lượng của các đường nối là rất quan trọng vì bất kỳ khiếm khuyết nào sẽ làm tổn hại đến tính toàn vẹn của hộp thiếc.
Các thành phần của một hộp thiếc điển hình có thể bao gồm
- Thân hình: Cơ thể chính của hộp thường được làm bằng thép hoặc tấm nhôm mỏng. Cơ thể được hình thành thành hình trụ và sau đó được hàn hoặc hàn lại với nhau để tạo ra một thùng chứa liền mạch.
- Kết thúc: Các đầu của hộp được làm bằng vật liệu đo dày hơn một chút so với cơ thể và thường được nối hoặc uốn trên cơ thể để tạo ra một con dấu an toàn. Kết thúc có thể là một kết thúc đơn giản hoặc một thiết kế phức tạp hơn, tùy thuộc vào yêu cầu của sản phẩm được đóng gói.
- Nắp: Nắp của lon là nắp trên cùng có thể được mở và đóng để truy cập vào nội dung của lon. Nắp có thể là một thiết kế có thể tháo rời hoặc không thể tháo rời, Tùy thuộc vào dự định sử dụng của lon. Nắp có thể tháo rời thường được sử dụng cho lon thực phẩm và đồ uống, trong khi nắp không thể tháo rời được sử dụng cho các vật liệu công nghiệp hoặc nguy hiểm.
- Đường may: Đường may là khớp kết nối cơ thể và phần cuối của lon. Đường may được tạo ra bằng cách lăn các cạnh của cơ thể và kết thúc lại với nhau và sau đó uốn hoặc nối chúng lại với nhau để tạo ra một con dấu an toàn.
- Lớp phủ: Lon thiếc có thể được phủ nhiều loại vật liệu để tăng cường tính chất của chúng và bảo vệ nội dung của lon. Lớp phủ chung bao gồm sơn mài, Lớp phủ polymer, và lớp phủ men.
- Nhãn: Nhãn được sử dụng để cung cấp thông tin về sản phẩm bên trong lon, bao gồm cả thương hiệu, thông tin dinh dưỡng, và chi tiết sản phẩm. Nhãn có thể được làm từ giấy, nhựa, hoặc kim loại và thường được dán vào cơ thể hoặc nắp của lon.
Một lựa chọn bền vững cho các thành phần có thể thiếc
Với sự tập trung ngày càng tăng vào tính bền vững và bao bì thân thiện với môi trường, Vật liệu tái chế được sử dụng trong sản xuất hộp thiếc. Bằng cách sử dụng thép hoặc nhôm có thể tái chế, Bạn có thể giảm tác động môi trường của bao bì của mình và giảm thiểu nhu cầu về nguyên liệu thô mới. Một lựa chọn bền vững khác là phát triển lớp phủ phân hủy sinh học cho lon thiếc. Những lớp phủ này được thiết kế để phá vỡ tự nhiên theo thời gian, Giảm tác động môi trường của lon thiếc bị loại bỏ
Các ứng dụng của TIN có thể thành phần trong các ngành công nghiệp khác nhau
Các bộ phận có thể có một loạt các ứng dụng trong các ngành công nghiệp khác nhau như:
Trong ngành công nghiệp thực phẩm
Lon thiếc thường được sử dụng để đóng gói trái cây đóng hộp, rau, súp và nước sốt. Độ bền và tính chất bảo vệ của lon thiếc giúp duy trì độ tươi và chất lượng thực phẩm, kéo dài thời hạn sử dụng của nó.
Công nghiệp hóa chất
Lon thiếc cũng được sử dụng trong các ngành công nghiệp như ô tô, Điện tử, và hóa chất công nghiệp. Trong các ngành công nghiệp này, Lon thiếc được sử dụng để đóng gói dầu động cơ, chất bôi trơn, chất kết dính, dung môi, và các sản phẩm công nghiệp khác. Độ bền và sức đề kháng của lon thiếc làm cho chúng phù hợp để chịu được môi trường khắc nghiệt và đảm bảo lưu trữ và vận chuyển an toàn của các hàng hóa này.
Tóm tắt
Sau khi đọc này, Bạn sẽ biết các thành phần thiếc có thể có bao nhiêu tác động trên lon thiếc. Các thành phần phù hợp không chỉ cho sự niêm phong và vẻ đẹp của hộp thiếc, nhưng cũng phải sử dụng các vật liệu bền vững để đóng góp để bảo vệ môi trường. Sự đóng góp, Hiểu những thành phần cơ bản này là rất quan trọng nếu bạn là nhà sản xuất đang tìm kiếm các sản phẩm thiếc chất lượng cao hoặc người tiêu dùng đang tìm cách đưa ra lựa chọn sáng suốt về hàng hóa đóng gói. Mặc dù lon thiếc là một giải pháp bao bì đáng tin cậy và bền vững, Sự hiểu biết về các thành phần của chúng có thể cải thiện hiệu quả và chức năng của các sản phẩm thiếc trong các ngành công nghiệp khác nhau.